- Visibility 92 Views
- Downloads 16 Downloads
- DOI 10.18231/j.jco.2022.022
-
CrossMark
- Citation
Fabrication of in-house aligner- A review
Introduction
Clear aligner technology marks a paradigm shift in orthodontics, upending conventional methods about how orthodontists move teeth.[1]
At the end of the 1990s, a computerised aligner system with promising characteristics was developed in the United States of America: Invisalign, which was conceived by two Stanford students, Zia Chishti and Kelsey Wirth. Since they were introduced to the market in 1999, clear aligners have evolved significantly.[2]
Align Technology's clear aligners are now comprised of a new tripolymer plastic and have optimised attachments. The teeth are repositioned using advanced computer algorithms built into the software package. Numerous clear aligner systems are being developed worldwide, and it is clear that this is the future of orthodontics.[3]
While the future of clear aligners is unknown, it is expected that a considerable emphasis will be placed on the following:
Aligners for use in practise, facilitated by the advancement of 3D printing.
Integration of computed tomography (CBCT with treatment planning software.
An increasing number of laboratories and companies that provide aligners.
Cost Reductions[4]
One of the primary drawbacks of aligners is how expensive and time intensive the entire procedure is. Additionally, shipping is a huge worry during these epidemic times. Thus, considering in house aligner production can only benefit both orthodontists and patients.
In-house aligners can be fabricated using an intra oral scanner and a generic aligner programming software for virtually trimming the models and simulation of movements. Once the aligner stages have been planned then each model file can be prepared for printing using a 3D printer. While the files can also be exported to a lab for printing, in house production has been shown to be cost effective over a prolonged period. Once the models are printed, a thermoforming machine is required in conjunction with a trimming handpiece Materials form a vital part of the in-house production, and polyethylene terephthalate has been shown to have the lowest deformation under variable conditions.[5]
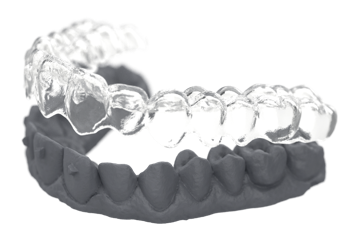
In-House Aligner Fabrication
Currently, the vast majority of clear aligners are planned and fabricated by submitting patient records (dental impressions, radiographs, clinical examination, and photographs, etc) to an external laboratory for appliance design and fabrication. This workflow describes companies like Invisalign, which also maintains all the data submitted to it for analysis to improve their treatment planning algorithms and to refine the services and products it offers. In addition, traditional orthodontic laboratories have started using aligner software to design and produce aligners as well.
A big advantage of Invisalign is the availability to the orthodontist of treatment libraries, which could be a guide for viewing similar aligner cases. On the other hand, the cost is significantly higher compared to in-house aligner design and fabrication. Presently, the cost of the necessary equipment for in-house aligner manufacturing (3D printer, thermoforming machine, intraoral scanner) is decreasing. Furthermore, with Invisalign and similar companies the orthodontist does not have the flexibility to easily alter the treatment plan or provide supplemental aligners when using outsourced clear aligner fabrication.
Advantages of in-house aligner fabrication
In-house aligner treatment affords the orthodontist the ability to check each stage of treatment and change its course accordingly. The ability to perform an intraoral scan as it is deemed necessary permits treatment assessment by superimposing the data on previous scans, as seen in. Another advantage of in-house aligner design is that some CAD software programs™ like Maestro Dental Studio™ offer an option to fuse a CBCT (converted to an STL format file) with the intraoral scan. This helps the orthodontist to visualize the dental roots while moving the crowns in the setup procedure.
The number of aligners that can be developed in the office is practically unlimited. The opposite is the case with aligner companies, where either a high price permits unlimited aligners or paying a lower fee allows only a limited number of aligners.
While in-house aligner fabrication requires the dedication of more doctor time and perhaps additional staff for aligner design and fabrication, in situations or clinical settings where access to external aligner companies is discontinued or limited (for example, during a pandemic lockdown), then the self-sufficiency of in-house aligner production is even more advantageous.
Staging the aligner treatment
Staging the tooth movements is another crucial part when designing aligner treatment, and with aligner CAD software™, staging is a procedure that often has to be included in the aligner design. Frequently, a combination of movements is required for each tooth to level and align. Often clinicians tend to design aligner treatments where these are all performed simultaneously.
However, in certain clinical situations, it has been shown to be more predictable to isolate these movements and execute them separately in a procedure called “staging.” Nevertheless, this staging concept requires more aligners to be fabricated.[5] For example, dental movements may be planned that result in areas of undercuts in order to serve as push surfaces for the plastic to generate forces. Think about bodily translation of a tooth. This can be broken into two separate movements: crown tipping and root uprighting. This is already an established concept used as the basis of the Begg technique and the modern Begg technique.[6]
When closing an extraction space with aligners, the plastic has no room to wrap around both interproximal surfaces of each tooth that will be bodily translated in the extraction space. If this is attempted, poor angulation control and poor tracking are observed. However, when this is done by first tipping the teeth into the extraction space, the plastic can then engage both their now-exposed mesial and distal interproximal surfaces, which will then be used to generate the couples to upright their roots A similar design can be implemented when distalizing a molar by letting it tip back first, enough for the plastic to be able to wrap around its mesial surface, and then uprighting its root. These tooth movements can be accompanied by just an extrusive attachment on the tooth to keep it within the plastic while these moments are applied.[7]
In-house aligner design
Generally, aligner treatment can be divided into three categories:
Full aligner treatment.
Hybrid aligner treatment, where treatment starts with fixed appliances and finishes using aligners (or the opposite).
Aligner treatment for relapse cases.
All orthodontic software programs share a similar workflow in clear aligner design. Some software packages also offer the ability to design aligners for direct 3D digital printing using aligner resin. The procedure of designing aligners was described using DeltaFace software™ without getting into details concerning biomechanical considerations. The software is easy and efficient to use, with plenty of tools to help the orthodontist design the necessary study models for aligner manufacturing or to design the aligners for direct 3D printing.[8]
Aligner Design Workflow Using an Orthodontic CAD Software ™
Intraoral Scan Importing
The first step is the digitization of the dental arches, usually using an intraoral scanner. A desktop scanner could be used in cases where polyvinyl siloxane impressions were taken. The impressions could be directly scanned, or plaster casts could be poured and scanned. All the necessary patient data were written down in the chart, and the intraoral scan of the dental arches were imported. Tools for capping, deleting, and smoothing can be used to clean up the scans of the dental arches.[9]
Occlusion Adjustment
The second step is to adjust the occlusion if needed. Nevertheless, most of the time the occlusion is defined correctly during intraoral scanning. Three points are selected on each arch to define and orient the occlusion plane to ensure that the digital model is in the right reference plane.[10]
Border Cleaning and Model Base Generation
In this stage, the borders of the virtual dental models should be cleaned automatically or manually, and the model bases are created to give the dental model its final form.[11]
Tooth Numbering and Segmentation
The fourth step is to define the teeth that will undergo segmentation by enabling them. After that, the software asks the operator to define the mesial and distal surfaces of each tooth.In this way, the software separates each tooth from its adjacent neighbour(s) and sets the default angle (rotation around Z) of the teeth. The last stage is segmentation. The software calculates and presents in different colors each tooth that is going to be moved in the setup stage. It is absolutely crucial to check every tooth. In case of incorrect segmentation, the operator can manually correct the problem.[12]
Defining Tooth Reference Axes
In this step, the operator adjusts the central point of the teeth. The central point of each tooth (red point) is the reference point used to measure all the rotations and translations in the setup stage. The software itself, through calculations, tries to define the approximate position of the root of each tooth in the space. Most of the time, this is not accurate. In two studies by Athanasiou and Halazonetis, it was shown that commercially available software cannot estimate the anterior tooth root inclination of digital models. For this reason, manual correction of the tooth axes must be performed. Importing the patient’s CBCT data is helpful in order to visualize the exact position of the roots. Unfortunately, radiation is an obstacle for CBCT scanning for many patients, unless it is needed for other medical reasons.[13]
Virtual Setup
The next step is the virtual setup of the dental arches. All software programs of this type have similar tools, and the teeth can be moved separately with the tooth manipulator or by defining the amount of movement or angulation change numerically. When teeth are virtually moved into an area lacking space, then IPR will be needed. When this is attempted, the software calculates and displays on the mesial and/or distal side of the tooth the space needed. The amount of IPR needed must be marked in the appropriate place within the software. One of the most important parts of CAT design is separating the teeth movements into stages. It is an error to do so in a single stage. The software cannot distinguish which teeth have to be moved first in order to have an efficient and smooth course of treatment.[11]
For instance, if we want to create space by distalizing the maxillary molars, we have to create different stages of movements. Movement of the molars has to be the first stage of the movement. Then a second stage has to be added where the crowded teeth are moved in the space created by the distalized molars In the current software, this can be done by using the “Add sequence” button. Careful planning and staging of individual and all tooth movements has to be performed in order to correctly guide the software. Staging can be visualized on the computer screen or printed onto paper in a PDF format. During the setup process, the attachments needed for these movements must be placed. A variety of attachments (elliptical, half-sphere, etc) are found in the appropriate library within the software. Their dimensions can be easily changed depending on the patient’s needs. Attachments can be placed on the teeth or “in” the teeth (negative attachment). Outsourced designed attachments can also be imported for use in the software.[14]
Furthermore, the strategic use of attachments as aligner anchorage points to stabilize the aligners during tooth movement is a critical role they play. Furthermore, the ability to use all the teeth as an anchorage against the movement of one or two teeth is a significant advantage of aligner treatment. The last stage is to add sequential labeling to each virtual model to be printed. It is useful to write the number on the buccal surface of the last molar that will not be moved so that each aligner will have its number printed. Once this sequence of setup stages has occurred, the operator can visualize the number of aligners that will be needed for the treatment. The maximum amount of movements (linear or angular change) that an aligner can perform is the same for every case. Nevertheless, there is an option to change the default numbers using a table provided. Concurrently, at this stage, a Bolton analysis is automatically created by the software.[12]
Exporting of Files
At this stage, the orthodontist has to define if the aligners will be printed on a 3D printer directly or if dental casts are to be printed from which aligners will be fabricated. If the latter is performed, the printed working models can be fabricated to be hollow and without bases in order to conserve material. However, care must be taken to avoid model breakage when removing it from the printer’s platform due to its reduced structural strength. In addition, models fabricated to be too thin may also distort during aligner thermoforming due to the heat involved in softening the aligner plastic material.[15]
Dental Model Printing
Undigitization The setup virtual dental models can now be printed—or undigitized and converted to a real object. Regarding the printing accuracy of study models, a study by Rebong et al showed that FDM (fused deposition modeling) casts had the fewest dimensional changes compared to plaster casts, while SLA and polyjet models had a tendency for expansion at the inter- and intra-arch measurements and a tendency for shrinkage at the vertical dimension.These results apply only to the specific resin, FDM filament, and to the particular printers that were used in the study. Generally, printing is done using SLA, DLP (digital light processing), or MSLA (masked stereolithography) printers, which all use dental model resin and a UV light source for polymerization (laser beam, light projector, or LCD light source).
The printing procedure is followed by the cleaning of the dental cast using isopropyl alcohol 91% and postprinting curing. FDM printers are less frequently used for working model printing. However, they have the advantage of a lower cost compared to the resin printing systems, and there is also no need for further post printing procedures. Isopropyl alcohol is also an irritant chemical substance, and therefore proper room ventilation is required. A disadvantage of FDM printer usage is the need for a special filament that can withstand the high temperature of the thermoforming procedure where deformation of the dental cast could lead to inaccurate aligner fabrication.[8]
Aligner Thermoforming
Following working model printing, aligner thermoforming is the next step. This procedure entails the use of vacuum or positive pressure thermoforming machines with various thermoforming plastic foils. Vacuum thermoforming machines cannot apply pressure of more than one bar (between 0–1 bar), which is the normal air pressure at sea level. However, positive thermoforming pressure machines have no limit on the amount of pressure they can exert. It is crucial to have a thermoforming machine that can deliver the proper pressure to create the aligners accurately. In cases where attachments are going to be placed on the teeth, a separate template aligner is developed by the software in order to facilitate attachment bonding. Usually, this is made of a thinner foil (eg, Duran 0.5 mm) to make template removal easier.
Tracking in any stage of the aligner treatment, the orthodontist can acquire a new intraoral scan to compare it with the initial intraoral scan using the superimposition feature. Superimposition can also be done between the new intraoral scan and the corresponding virtual dental cast.
In this way, the orthodontist can check whether the specific aligner at this stage is moving the teeth exactly as it was designed. In the case that refinement aligners are needed, the orthodontist can proceed to the setup tool and add a new “stage” of treatment, which will allow for further tooth movements. In-house aligner design and fabrication is a multiple-step procedure that the orthodontist has to fulfill. Intraoral scanning, clinical examination, the taking of radiographs and clinical photographs, CAD software™ use, dental model 3D printing, and thermoforming of the aligners are the stages that are essential for a successful treatment outcome.[16]
On the other hand, in an orthodontic laboratory, the technician assumes a more significant role in aligner design and fabrication while the orthodontist plays a lesser role. Aligner companies unavoidably take the biggest piece of the pie in the design and fabrication of the aligners (see). It is the clinician’s decision whether to be in charge of all the aligner design-printing procedure, have a laboratory do a part of this, or have an aligner company provide complete service in this endeavor.[17]
Conclusion
In-house aligner design and printing provide numerous advantages. It is time for orthodontists to avail themselves of these and be fully in charge of the aligner orthodontic treatment. There is a movement toward in-house aligner design and printing that is reflected by the emergence of new companies that develop aligner software, dental 3D printers, intraoral scanners, new thermoforming materials, and as of late, resin for direct aligner printing. Nevertheless, even with the plethora of materials and machines for aligner designing and printing, aligner treatment is still minimally investigated. Incorporating in-house aligner fabrication by orthodontist can be a game changer in the field of orthodontics.
However, Biology is kept out of the designing procedure, which is carried out without taking into account the surrounding tissues and the tooth-root structure itself. Tooth movement–simulating software works as if there is no underlying tissue, no bone, no roots, no gingiva, and no occlusion. Future studies should focus on these inadequately investigated parameters.[18]
Source of Funding
None.
Conflict of Interest
None.
References
- P Jindal, M Juneja, F L Siena, D Bajaj, P Breedon. Mechanical and geometric properties of thermoformed and 3D printed clear dental aligners. Am J Orthod Dentofac Orthop 2019. [Google Scholar]
- L J Zafra, P S Moya. Aligner techniques in Orthodontics. 2021. [Google Scholar]
- PH Buschang, SG Shaw, M Ross, D Crosby, PM Campbell. Comparative time efficiency of aligner therapy and conventional edgewise braces. Angle Orthod 2014. [Google Scholar]
- S Tai. Clear Aligner Technique. 2018. [Google Scholar]
- P C Kesling. Expanding the horizons of the edgewise arch wire slot. Am J Orthod Dentofac Orthop 1986. [Google Scholar]
- P R Begg, P C Kesling. Begg Orthodontic Theory and Technique. 1977. [Google Scholar]
- L Robertson, H Kaur, N Fagundes, D Romanyk, P Major, F Mir, C. Effectiveness of clear aligner therapy for orthodontic treatment: A systematic review. Orthod Craniofac Res 2020. [Google Scholar]
- N C Panayi. In-house customization of lingual orthodontic brackets using Ubrackets computer-aided design orthodontic software. Clin Tecthniques 2021. [Google Scholar]
- G Rossini, S Parrini, T Castroflorio, A Deregibus, C Debernardi. Efficacy of clear aligners in controlling orthodontic tooth movement: A systematic review. Angle Orthod 2014. [Google Scholar]
- M Dastoori, J Bouserhal, D Halazonetis, A Athanasiou. Anterior teeth root inclination prediction derived from digital models:A comparative study of plaster study casts and CBCT images. J Clin Exp Dent 2018. [Google Scholar]
- P M Trikka, D Halazonetis, A Athanasiou. Estimationof root inclination of anterior teeth from virtual study models: Accuracy of a commercial software. Prog Orthod 2019. [Google Scholar]
- W Bolton. The clinical application of a tooth-size analysis. Am J Orthod 1962. [Google Scholar]
- R Rebong, K Stewart, A Utreja, A Ghoneima. Accuracy of three-dimensional dental resin models created by fused deposition modeling, stereolithography, and Polyjet prototype technologies: A comparative study. Angle Orthod 2018. [Google Scholar]
- L Camardella, O De Vasconcellos Vilella, H Breuning. Accuracyvof printed dental models made with 2 prototype technologiesand different designs of model bases. Am J Orthod Dentofac Orthop 2017. [Google Scholar]
- E Chan, N Panayi, G Polychronis. In-house 3D-printed aligners: effect of in vivo ageing on mechanical properties. Eur J Orthod 2022. [Google Scholar]
- J Weckmann, S Scharf, I Graf. Influence of attachment bonding protocol on precision of the attachment in aligner treatments. J Orofac Orthop 2019. [Google Scholar]
- A Papadopoulou, A Cantele, G Polychronis, S Zinelis. Eliades Changes in roughness and mechanical properties of Invisalign appliances after one- and two-weeks use. Materials 2019. [Google Scholar]
- M Tozlu, F Ozdemir. In-house Aligners: Why We Should Fabricate Aligners in Our Clinics?. Turkish J Orthod 2021. [Google Scholar]
- Introduction
- Cost Reductions[4]
- In-House Aligner Fabrication
- Intraoral Scan Importing
- Occlusion Adjustment
- Border Cleaning and Model Base Generation
- Tooth Numbering and Segmentation
- Defining Tooth Reference Axes
- Virtual Setup
- Exporting of Files
- Dental Model Printing
- Aligner Thermoforming
- Conclusion
- Source of Funding
- Conflict of Interest